精益生产,APS生产计划排程系统应用-缩短制造周期
精益生产4个基本目标: 高设备利用率、低库存、生产周期短、按时交货。要实现这4个目标,需要借助软件工具,否则即便有改善的意愿,也没有可行性。
本文探讨APS在生产周期管理方面的应用。缩短产品制造周期可以大大降低在制品的数量,减少半成品库存,并避免产生半成品呆料。
生产周期过长的危害很多,总结有几点:
- 对于成品和零部件都由本厂生产的企业,零部件生产时间过长, 容易引发零件库存过高,产生呆料。如果零部件提前多日开始生产,总装计划发生变更时,零部件就会变成库存。
- 车间的在制品数据过大,线边堆积了大量的半成品,占用空间。由于不能及时入库,难以管理,也很难做到先入先出,容易引发品质问题。
为什么会有生产周期过长的问题?
理论上,工序之间时间关系应尽量紧密,只要满足运输要求就可以安排生产。
在实际上,因为工厂采用手工方式排程,计划员无法精确计算每个工序之间的延时。设备共用,各产品工序纵横交错,如果一个设备发生故障,或者客户变更订单,整个计划就全盘打乱。
计划员人工方式编制的生产计划如下:
假设产品生产需要3个工序,作为示例,我们简化生产工艺,令各工序生产时间一样
计划员手排的计划通常如下:
假设设备每天工作11小时,对于需要三个生产工序的产品,
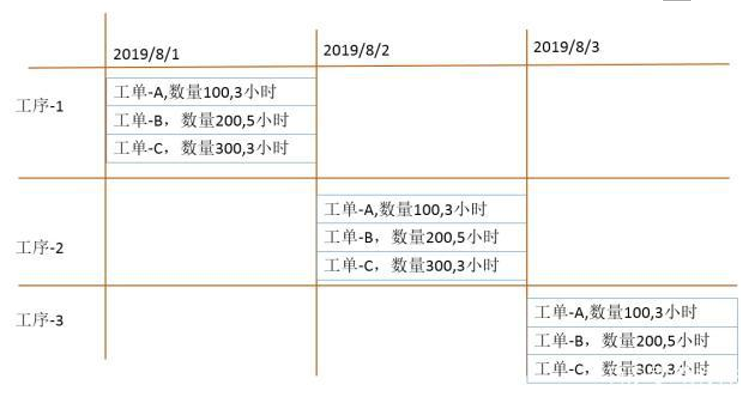
从上图中可以看到,产品生产共需要3天时间。
为什么PMC要这样排程? 因为Excel无法精确计算工序之间的缓冲时间,简化的做法就是拉长工序延迟,通常工序间间隔1-2个班次是常见做法。将下道工序放到下个班次,计划员只需要排出生产顺序和计算本班次总的工作时间可生产的工单,而不需要计算下个工序何时开始。 如果一个订单生产发生异常,计划员也比较容易修改计划。
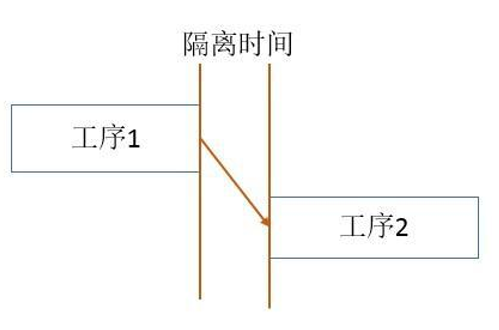
在我们实施过的APS项目中,导入APS前,工序间延迟大部分在12小时以上。导入APS后,工序延迟缩短到2-4小时。 生产周期缩短,车间的在制品数量将大大减少,降低了管理成本,同时也降低了半成品库存水平。
产品生产周期的缩短,对于生产工序多的企业,效果最为显著。